Rivestimento lavorante
Confronto dei metodi di costruzione di una fusoliera di un aereo,
1: traliccio con tela,
2: traliccio con lamiera ondulata,
3: costruzione a guscio,
4: costruzione a semiguscio
Stressed skin ( pelle stressata)
In ambito ingegneristico, e in particolare nell’aviazione, nell’edilizia e nell’automobilismo, si definisce rivestimento lavorante (o resistente) quel tipo di copertura esterna di una struttura interna che assorbe parte dei carichi strutturali a cui la costruzione, nel suo complesso, è soggetta. In contrapposizione alle strutture in cui un rivestimento passivo è applicato a una struttura resistente, una struttura a rivestimento lavorante delega in parte al rivestimento esterno la funzione attiva di assicurare al tutto robustezza e rigidezza.
Un rivestimento lavorante è tipicamente una componente essenziale delle strutture dette “a semiguscio”, in cui i carichi sono assorbiti in parte dalla struttura interna e in parte dal rivestimento esterno; tale genere di strutture si colloca a metà strada tra quelle in cui il rivestimento è interamente passivo e le funzioni strutturali sono affidate esclusivamente alla struttura interna e quelle, dette “a guscio”, in cui i carichi sono interamente assorbiti dal rivestimento esterno.
In campo edilizio, in generale, l’impiego di strutture interne resistenti rivestite da coperture passive è più economico rispetto all’impiego di rivestimenti lavoranti come potrebbero essere muri o soffitti in cemento armato. Rivestimenti lavoranti sono cionondimeno utilizzati in alcune di quelle circostanze in cui si rendono necessari per ragioni di ordine estetico
A_ COSTRUZIONE A SEMIGUSCIO
Con costruzione a semiguscio ( pelle stressata in inglese o semi-monoscocca ) un metodo di costruzione per la costruzione di fusoliere di aerei e razzi , e più raramente anche di ali , viene indicato nella costruzione di aeromobili , in cui la “resistenza” della pelle esterna (fasciame) di questi componenti è dimensionata in modo che Può assorbire la maggior parte delle forze che si verificano. Rispetto alla costruzione a guscio puro ( monoscocca ) , che riesce senza rinforzi interni o con poco rinforzo tramite nervature trasversali , la costruzione a semiguscio utilizza anche rinforzi longitudinali. Questi sono tipici Longerons (longheroni del busto) e traverse ( longheroni più deboli), che aiutano ad alleviare la pelle esterna. Questo per rimediare al principale punto debole della costruzione monoscocca pura, vale a dire ottenere una resistenza sufficiente con il minor peso possibile. Tuttavia, una distinzione coerente tra i termini costruzione a conchiglia e semiguscio non può essere riconosciuta in letteratura. Spesso entrambi i termini sono usati come sinonimi. Occasionalmente, la struttura a guscio, basata sulla carrozzeria autoportante dei veicoli, viene anche definita struttura autoportante.
La Storia
Il primo utilizzo comprovato della costruzione monoscocca fu presentato all’Olympia Aero Show del 1911 con una macchina progettata da Handley-Page. I
l guscio della fusoliera di tipo D (denominato retroattivamente HP4 nel 1924) era costituito principalmente da legno di mogano .
Altre prime applicazioni della costruzione del guscio nella costruzione di aeromobili sono il Deperdussin Monocoque Racer del 1912, come un altro esempio della costruzione in legno inizialmente utilizzata. Lo scafo del Loughead S-1 del 1919 progettato da Jack Northrop è stato realizzato in due stampi di cemento. Qui lo scafo era costituito da diversi strati di compensato. Esempi tipici in Germania furono l’ Albatros DV della prima guerra mondiale e il più tardi costruito Heinkel He 70 .
Dornier fece i primi tentativi con una costruzione a conchiglia interamente in metallo nel 1917 con la Dornier Cl.I , in cui la costruzione a conchiglia in legno della biposto Albatros doveva essere trasferita alla costruzione in metallo.
La misura in cui lo scafo della fusoliera era realmente in grado di assorbire forze non è, tuttavia, chiara. I primi aerei effettivamente progettati con una struttura interamente in metallo furono il Dornier Zeppelin DI , che volò per la prima volta nel giugno 1918, e lo Short Silver Streak, che fu mostrato all’Olympic Airshow nel luglio 1920 .
Alla fine degli anni ’60, nella costruzione degli alianti prevaleva la costruzione della scocca con materiali compositi in fibra di vetro. Quindi il peso potrebbe essere ridotto. Per lo stesso motivo, le plastiche rinforzate con fibra di carbonio (“carbonio”) vengono sempre più utilizzate nella costruzione di aeromobili commerciali
Esecuzione costruttiva
Generale
Nel caso di costruzione a semiguscio, una sottostruttura composta da longheroni, traverse , telai / paratie viene solitamente utilizzata per rinforzare la pelle esterna e per mantenere la forma della sezione trasversale e formatori. Le forze di flessione che agiscono sul tronco vengono assorbite dai Longerons che corrono paralleli alla direzione longitudinale del tronco. I longheroni hanno una sezione trasversale più piccola dei longheroni e li aiutano ad assorbire le forze di compressione e ad aumentare la rigidità dello scafo. I telai e le paratie vengono utilizzati principalmente per mantenere la forma della sezione trasversale e aumentare la stabilità delle traverse contro l’attorcigliamento. Le paratie sono preferite dove le forze sono concentrate nella fusoliera o nelle ali. Questi sono ad es. B. supporti del motore, collegamenti alari, arresto del carrello di atterraggio e collegamenti delle alette di coda.
La divisione in telai e traverse è anche chiamata “straken” nel termine tecnico.
Oltre a utilizzare il modulo ad alta sezione delle sezioni trasversali della fusoliera a cerchio chiuso, il vantaggio principale della costruzione a guscio o semiguscio rispetto alla fusoliera a traliccio è la possibilità di ottenere una fusoliera progettata aerodinamicamente senza dover utilizzare componenti di sagomatura aggiuntivi. Inoltre, l’interno può essere completamente utilizzato poiché non ci sono montanti o fili di rinforzo.
La produzione pratica di solito avviene in più gusci singoli che vengono rivettati o incollati insieme per formare una sezione trasversale quasi rotonda o ovale.
I ritagli nella struttura del guscio rappresentano una sfida, per cui la parte centrale centrale del guscio è preferibilmente coperta da porte, portelli, ecc. dovrebbe essere mantenuto libero. Ad esempio, nel caso del Vought F-8 , che non aveva rinforzi longitudinali, non era possibile aprire tutti i portelli di manutenzione contemporaneamente durante la manutenzione, poiché altrimenti la fusoliera si sarebbe deformata durante lo spostamento dell’aereo.
Costruzione in legno
Nella costruzione in legno, diversi strati di compensato, per lo più in diversi spessori, vengono solitamente incollati uno sopra l’altro e uno accanto all’altro con l’aiuto di uno stampo positivo. Con il Loughead S-1 , invece, è stato utilizzato un airbag in uno stampo negativo, che è stato gonfiato dopo che lo stampo è stato chiuso e tenuto sotto pressione per 24 ore.
Nei moduli per il Lockheed Vega si poteva stabilire il airbag per tre diversi modelli.
A seconda della posizione e della forma delle aperture ricavate nel guscio, oltre al Vega potrebbero essere prodotti anche l’ Air Express o l’aereo ad ala bassa Sirius .
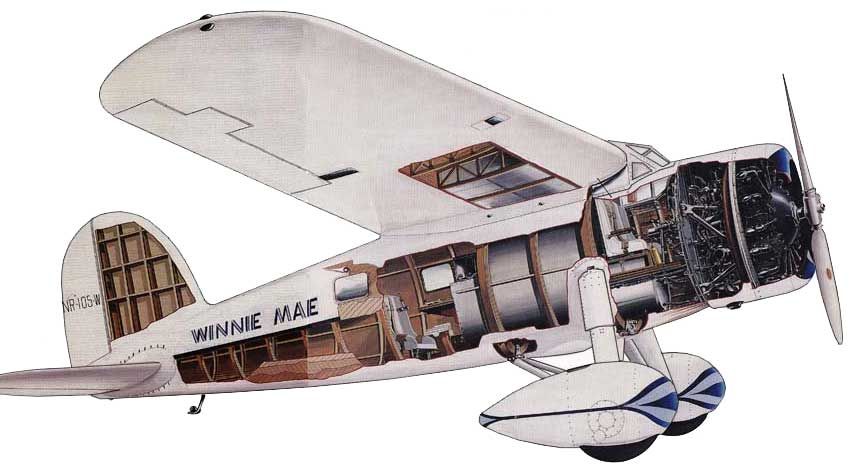
Vega risultava avere un aspetto, oltre alle soluzioni tecniche adottate, particolarmente moderno. La fusoliera era monoscocca, realizzata con una struttura in legno su cui erano posti pannelli di compensato.
Usando uno stampo in calcestruzzo, lo strato della mezza semi-fusoliera laminata veniva unita utilizzando un collante, quindi, grazie ad una camera d’aria inserita nella struttura e quindi gonfiata, questa veniva compressa favorendo la completa adesione delle parti. Le due metà venivano successivamente inchiodate ed incollate su un telaio precedentemente realizzato.
I tipi di legno.
Vengono utilizzati abete Sitka , betulla , mogano e legno di tulipano . Il legno di balsa viene utilizzato anche negli strati intermedi . Gli adesivi tipici sono la colla alla caseina storicamente interessante e l’attuale Aerodux sintetico.
Esempio Mosquito
Lo scafo del De Havilland DH.98 Mosquito è stato fabbricato come una monoscocca in due semigusci, che sono stati gestiti con alcuni irrigidimenti longitudinali. Né la pressione né il calore erano necessari per fabbricare le ciotole. Le due forme positive, lunghe circa 12 m, erano realizzate in legno di mogano.
Nella produzione canadese vengono utilizzati anche stampi in calcestruzzo.
Nella prima fase di costruzione, le paratie dello scafo e altri elementi interni sono stati inseriti nelle fessure dello stampo. Nella seconda fase, è stata posata la pelle interna dello scafo e sono stati installati i componenti strutturali tra gli strati di compensato interno ed esterno. Nella parte posteriore della fusoliera, le strisce di compensato sono state incollate ad angolo per poter assorbire meglio le forze derivanti dal carico torsionale causato dal gruppo di coda. La grana delle strisce interne ed esterne correva in direzioni opposte.
Costruzione in alluminio o metallo
Planking
Il rivestimento esterno è solitamente costituito da un foglio di alluminio laminato di qualità speciale. Viene teso su una macchina allungatrice con cinghie su un dispositivo corrispondente alla forma della fusoliera dell’aereo e quindi portato in forma. La struttura laminata viene migliorata anche mediante allungamento . Prima della rivettatura, il foglio esterno viene solitamente portato allo spessore desiderato in un bagno acido. Una vernice protettiva viene applicata nei punti in cui la lastra deve mantenere il suo intero spessore (ad esempio nell’area di finestre, porte, telai e traversi). In luoghi senza vernice protettiva, il foglio di alluminio viene rimosso chimicamente dall’acido. Il tempo di incisione controlla esattamente lo spessore.
Assemblaggio dei semigusci
I semigusci finiti vengono rivettati ai rispettivi telai e le lamiere esterne con l’altro semiguscio coordinato. Le sezioni di fusoliera risultanti sono rivettate longitudinalmente alle traverse e ai pannelli esterni. A causa della leggera sovrapposizione dei traversi, dei telai e dei fogli esterni durante la rivettatura, questi collegamenti hanno quasi esattamente la stessa resistenza di un segmento circolare, sono solo leggermente più pesanti, ma sono significativamente più economici da produrre.
Grandi assiemi
Gli aerei commerciali di grandi dimensioni con uno o due corridoi centrali nella cabina di solito hanno una sezione trasversale circolare e sono spesso fabbricati in tre gusci. Ciò consente un trasporto marittimo, aereo o stradale economico dai fornitori alla sala di assemblaggio finale e uno stoccaggio intermedio salvaspazio e quindi poco costoso.
Protezione dalla corrosione
Gli aeromobili sono soggetti a notevoli fluttuazioni di temperatura durante il funzionamento. Livelli di umidità fino al 100% e temperature superiori a 40 ° C possono spesso essere trovati su un aeroporto tropicale . Ad altitudine di crociera (spesso +12.000 m) le temperature esterne sono dell’ordine di -55 ° C circa. Questo e la continua evaporazione nella cabina passeggeri portano a una forte formazione di condensa e quindi a una grave corrosione. Pertanto, tutte le parti in alluminio devono essere sgrassate e verniciate prima del montaggio. Uno strato intermedio gommoso deve essere applicato tra i telai, traverse e lamiere prima del montaggio. Dopo la rivettatura, tutti i collegamenti vengono nuovamente rivestiti con vernice anticorrosione. Queste misure sono standard nell’odierna costruzione internazionale di aeromobili in metallo e garantiscono una normale vita utile e una vita operativa di circa 15–40 anni.
Esempio Bf 109
Schema di costruzione del guscio Bf-109
Dalla sezione dell’abitacolo in poi, la fusoliera del Messerschmitt Bf 109 è una costruzione a semiguscio ottimizzata soprattutto in vista della produzione industriale di massa. Ad esempio, i telai sono stati integrati nei singoli elementi di rivestimento piegando i bordi ( flangiatura ) durante la produzione. Questa lavorazione doveva essere eseguita solo sulla metà dei segmenti (numerazione pari) su entrambi i lati. L’altra metà degli otto fogli di rivestimento sono stati progettati come semplici fogli piatti. Non era più necessario rivettare nervature aggiuntive per l’irrigidimento. Durante la costruzione della fusoliera, tutti i segmenti di lamiera di una metà della fusoliera sono stati allungati su una falsa struttura e rivettati insieme. Le traverse sono state quindi spinte attraverso cavità predisposte nelle “curve del telaio” e rivettate alla pelle esterna in duralluminio spesso 0,8 mm. Le due metà della fusoliera sono state quindi unite insieme rivettando un’ulteriore traversa extra larga dall’alto e dal basso.
Materiali compositi in fibra: GRP e CFRP
Principio e materiale
Le plastiche rinforzate con vetro (GRP) o fibra di carbonio (CFRP) sono state a lungo materiali provati e testati nella costruzione di alianti e barche e sono ora sempre più utilizzate negli aerei commerciali tramite l’aviazione militare (qui: carbonio) . Un materiale di supporto, di solito un bicomponente – resina costituita da resina più una quantità accuratamente dosata di indurente, le parti assorbono forze di spinta. Un materiale in fibra (come fibra di vetro o carbonio) assorbe le sollecitazioni di trazione. Poiché il vetro e soprattutto le fibre di carbonio possono assorbire sollecitazioni di trazione molto elevate con poca deformazione, le parti realizzate con questo materiale hanno una rigidità e una resistenza maggiori rispetto a quelle realizzate in alluminio con una massa inferiore . Quindi una combinazione di due materiali diversi diventa una nuova con i vantaggi di entrambi i materiali combinati. Tuttavia, poiché il materiale è fragile, sono necessari nuovi processi e metodi per garantire la tenacità, che è estremamente importante per la costruzione di aeromobili.
Dimensione della sezione
Nel caso dei materiali compositi, si cerca di costruire i componenti più grandi possibile in un unico pezzo, poiché ogni punto di connessione deve essere collegato in modo complesso e sovrapposto ed è quindi un punto debole e di costo. Quando si costruiscono alianti, l’intera fusoliera dalla cabina di pilotaggio alla coda verticale è solitamente laminata in un unico pezzo. Per componenti di grandi dimensioni, come B. Con il moderno Boeing B787 , per ragioni economiche (vedi sopra), l’intero velivolo non può essere laminato “in un unico pezzo”. Con tali dimensioni, i gruppi utili (sezioni) vengono nuovamente formati.
Forma positiva / negativa
La forma positiva della fusoliera dell’aereo viene invertita e prodotta direttamente come forma negativa o modellata da un cosiddetto modello master . Questa forma viene trattata con una cera distaccante per evitare che il materiale si attacchi alla forma. Il primo strato di resina bicomponente o uno speciale primo strato di riempimento viene applicato e successivamente forma la pelle esterna. In questo strato viene posizionato uno strato di fibra di vetro o di carbonio. In cima a questo c’è un altro strato di materiale in fibra. Il livello successivo è ora inserito con un’angolazione diversa (spesso incrociando quella inferiore). Con prototipi o piccole serie a mano, con serie medie con il supporto di un dispositivo di marcatura laser (inglese: ” Scanner“) E per grandi serie con un robot di laminazione. Strato per strato, vengono costruiti tra 5 e 20 strati. Questo deve essere fatto in tempi relativamente brevi, poiché il tempo di “colla aperta” scade molto presto dopo che la resina e l’indurente sono stati miscelati insieme. La pelle esterna è molto liscia dopo la sformatura e deve essere lavorata solo in minima parte. L’interno è spesso ruvido e irregolare. Nello stampo sono già ricavate aperture più grandi per porte, finestre o ribalte e l’elevata rigidità e resistenza tangenziale a essa richiesta si ottiene posando le fibre del laminato secondo il profilo.
Cornici e traverse
In luoghi con carichi particolarmente elevati come motori , carrelli di atterraggio o supporti alari , nonché nella costruzione di aeromobili in metallo e legno, le paratie, i telai e, se necessario, i traversi sono installati come rinforzi. Questi sono incollati alla pelle esterna in diversi strati negli angoli.
Direzione di laminazione e numero di strati
Poiché (idealmente) le curve di sollecitazione nella fusoliera sono note in anticipo attraverso prove con celle di frattura o metodi FEM , il numero di strati e la direzione delle strisce di fibre possono essere determinati in anticipo. Maggiore è la tensione prevista, più strati. L’angolo tra gli strati determina in gran parte la resistenza ed è determinato in complesse simulazioni numeriche .
Assemblaggio
I semigusci così modellati presentano una sporgenza dopo la sformatura che deve essere rimossa. Per scollegare , eliminando così il margine in eccesso, solitamente a 5 assi si utilizzano macchine HSC – fresatrici – o macchine da taglio a getto d’acqua . In speciali dispositivi di assemblaggio, gli elementi del guscio sono allineati, fissati e incollati tra loro con strati aggiuntivi di resina più materiale in fibra in modo che si sovrappongano.
Impatto ambientale, riparazione, riciclaggio
Esistono cicli materiali funzionanti per l’alluminio . Per i materiali compositi in fibra fragile, queste procedure di manutenzione devono ancora essere sviluppate o stabilite in un’ampia applicazione. La riparazione conveniente di ammaccature, ammaccature o persino buchi che si verificano rapidamente negli aeroporti di tutti i giorni a causa di collisioni con veicoli terrestri deve ancora essere ottimizzata. Tuttavia, il vantaggio in termini di peso supera questo svantaggio grazie al risparmio di carburante. Le compagnie di assicurazione non hanno ancora valori empirici affidabili ovunque.
Esempio Airbus A350
Per l’ Airbus A350 viene utilizzata una costruzione mista di leghe di alluminio e CFRP, con CFRP che rappresenta il 52% del totale degli aeromobili. Una sezione della fusoliera dell’Airbus A350 è composta da quattro singoli elementi CFRP che sono rivettati su telai in alluminio. Anche le traverse dell’A350 sono realizzate in CFRP e sono incollate al rivestimento esterno in una fase di lavoro precedente.
Spazio
Anche i grandi razzi per i viaggi spaziali sono per lo più fabbricati con struttura a semiguscio. Uno dei primi razzi di questo tipo fu il razzo V2 verso la fine della seconda guerra mondiale. Era diviso in quattro assemblee più grandi :
- Trasmissione (con motore, carenatura, quattro superfici di controllo)
- Scafo costituito da due grandi semigusci rivettati insieme
- due serbatoi comprensivi di tubazioni per carburante e ossigeno
- Punta con controlli di volo e testata
I due semigusci e i due serbatoi furono prodotti dal 1943 al 1945 a Saulgau, nel Württemberg, lontano dall’assemblaggio finale.
Altre aree di applicazione
Silenziatore per la costruzione del veicolo
I silenziatori nel sistema di scarico sono corpi cavi che di solito sono costituiti da due gusci di lamiera imbutita. Questi sono fissati in dispositivi di saldatura e saldati insieme
Rivestimento lavorante
Il rivestimento in lamiera ondulata di un Junkers Ju 52. Gli aerei Junkers furono tra i primi, già a partire dalla fine della prima guerra mondiale, a impiegare soluzioni costruttive interamente metalliche con rivestimento lavorante.
In ambito ingegneristico, e in particolare nell’aviazione, nell’edilizia e nell’automobilismo, si definisce rivestimento lavorante (o resistente) quel tipo di copertura esterna di una struttura interna che assorbe parte dei carichi strutturali a cui la costruzione, nel suo complesso, è soggetta. In contrapposizione alle strutture in cui un rivestimento passivo è applicato a una struttura resistente, una struttura a rivestimento lavorante delega in parte al rivestimento esterno la funzione attiva di assicurare al tutto robustezza e rigidezza.
Aviazione
In aviazione, l’impiego di rivestimenti lavoranti cominciò a diffondersi a partire dal periodo compreso tra la prima e la seconda guerra mondiale. I velivoli delle prime generazioni erano caratterizzati, in generale, da una costruzione basata su una struttura lignea resistente rivestita da tela verniciata; questo tipo di rivestimento svolgeva una funzione puramente aerodinamica: costituiva infatti le superfici portanti delle ali e le superfici di controllo degli impennaggi, contribuendo inoltre a ridurre la resistenza opposta all’avanzamento dalla fusoliera (la cui struttura altrimenti sarebbe rimasta scoperta), ma non svolgeva alcun ruolo strutturale. La graduale diffusione dapprima dei rivestimenti in legno compensato e poi, soprattutto, delle costruzioni interamente metalliche con rivestimenti a loro volta metallici consentì ai progettisti di aeroplani di demandare parte delle funzioni resistenti al rivestimento stesso, riducendo così il peso e la complessità delle strutture interne (ordinate, correnti, longheroni e centine) a cui il rivestimento è, comunque, vincolato. Un ulteriore vantaggio dei rivestimenti lavoranti (lignei o, più spesso, metallici) risiede nel fatto che essi, essendo per l’appunto rigidi, garantiscono una migliore aderenza della sezione delle ali al profilo alare voluto, migliorando l’efficienza delle superfici aerodinamiche.
Un rivestimento lavorante è tipicamente una componente essenziale delle strutture dette “a semiguscio”, in cui i carichi sono assorbiti in parte dalla struttura interna e in parte dal rivestimento esterno; tale genere di strutture si colloca a metà strada tra quelle in cui il rivestimento è interamente passivo e le funzioni strutturali sono affidate esclusivamente alla struttura interna e quelle, dette “a guscio”, in cui i carichi sono interamente assorbiti dal rivestimento esterno.
Edilizia
In campo edilizio, in generale, l’impiego di strutture interne resistenti rivestite da coperture passive è più economico rispetto all’impiego di rivestimenti lavoranti come potrebbero essere muri o soffitti in cemento armato. Rivestimenti lavoranti sono cionondimeno utilizzati in alcune di quelle circostanze in cui si rendono necessari per ragioni di ordine estetico.
Automobilismo
In ambito automobilistico le esigenze di leggerezza e robustezza che si manifestano in sede di progettazione dei veicoli, congiuntamente con la necessità di conservare uno spazio libero il più ampio possibile al loro interno, rendono spesso conveniente fare ricorso a strutture con rivestimento lavorante. Le strutture automobilistiche in cui gran parte dei carichi sono assorbiti da una struttura esterna resistente sono dette “a monoscocca”, mentre nei casi in cui il rivestimento (comunque portante) è rinforzato da strutture interne si parla di strutture “a semi-monoscocca”.
ELEMENTI
Il correntino
Nelle costruzioni aeronautiche il corrente (o correntino, in inglese, stringer ) è un irrigidimento longitudinale che contribuisce a rinforzare il rivestimento lavorante nelle strutture a guscio quali ali e fusoliere.
Nella maggior parte dei moderni aerei da trasporto, i correntini sono costituiti da profilati metallici in leghe aeronautiche che sono rivettati al rivestimento lavorante. Nel Boeing 787, invece, il rivestimento esterno (skin) ed i correntini (entrambi in materiale composito) sono saldati assieme durante la fase di polimerizzazione ad alta temperatura in autoclave.
In una struttura di fusoliera tipo semi-monoscocca, il correntino è l’elemento strutturale dedicato ad assorbire gli sforzi indotti dalle flessioni così come le ordinate (trasversali) hanno la funzione di mantenere la forma del rivestimento esterno e possono essere o meno solidali ai correnti. Il rivestimento esterno, invece, assorbe le sollecitazioni dovute alla pressurizzazione e alla torsione.
Nelle ali, i correntini trasferiscono i carichi di flessione agli elementi trasversali chiamati centine che, a loro volta, li distribuiscono sui longheroni principali mentre il rivestimento lavorante sopporta le sollecitazioni torsionali.
I correntini si differenziano dai longheroni (anch’essi deputati a sopportare i carichi di flessione) per il loro maggior numero e minori sezioni a parità di carichi.
LINK
https://de.wikipedia.org/wiki/Zollingerdach
https://de.wikipedia.org/wiki/Schalentheorie
https://de.wikipedia.org/wiki/H%C3%BClle
http://classes.belem44.free.fr/guemene/site%20Belem/les_tcechnik..htm
https://de.wikipedia.org/wiki/Halbschalenbauweise
https://it.wikipedia.org/wiki/Cupola_geodetica
Se hai problemi per affrontare i punti suindicati, e vuoi ottimizzare i tempi, potresti valutare la possibilità di frequentare un corso per la preparazione dell'esame di stato di architetto o singole lezioni su ogni argomento legato alla professione di Architetto / Pianificatore Territoriale e/o alla prova d’esame.
________________________________________________________________________ _________________________________________________________________________Pubblicazione gratuita di libera circolazione. Gli Autori non sono soggetti a compensi per le loro opere. Se per errore qualche testo o immagine fosse pubblicato in via inappropriata chiediamo agli Autori di segnalarci il fatto è provvederemo alla sua cancellazione dal sito